The construction industry’s latest challenge doesn’t come in the form of a dip in the economy or shortage of labor.
This year, the U.S. Occupational Safety and Health Administration (OSHA) set a new standard in order to reduce worker exposure to crystalline silica. The new standard says exposure cannot exceed 50 micrograms per cubic meter (50 µg/m³) in an eight-hour day; that compares to the prior standard of 200 micrograms.
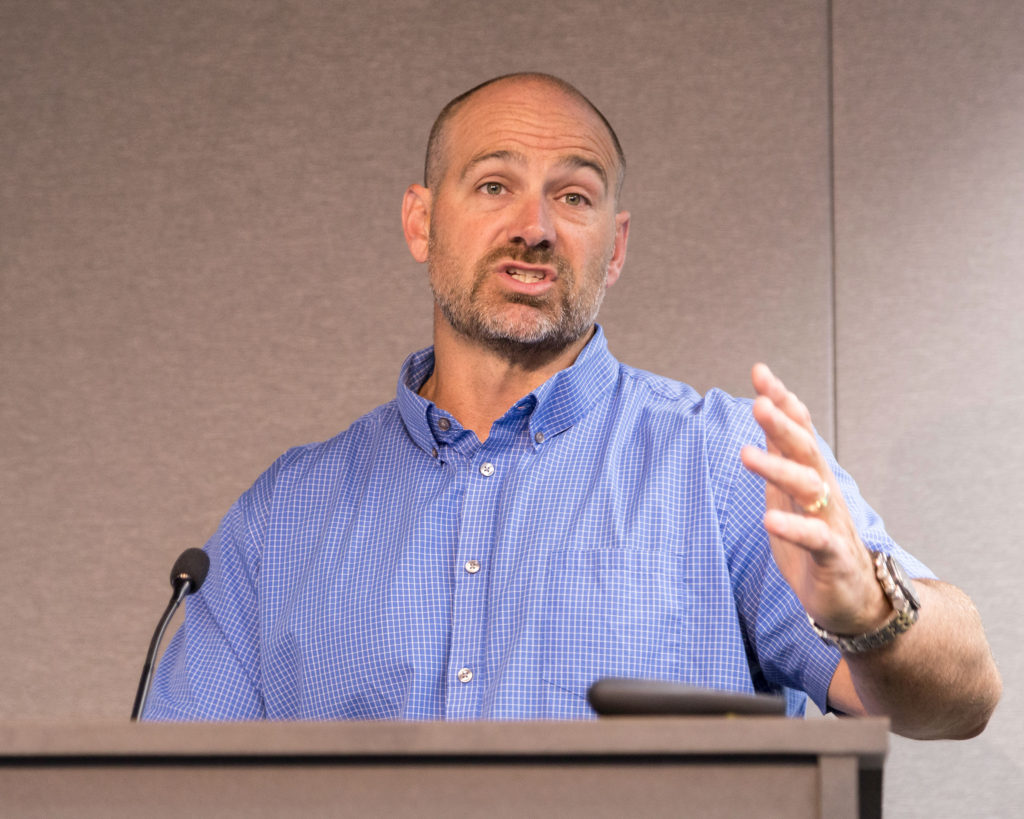
“The permissible exposure level has been cut down dramatically,” Ken Lindberg, risk control specialist with Travelers Insurance, told a gathering of Walbridge operations and estimating personnel in October. “You now need to determine what operations generate silica dust and how much; and you need to come up with a plan to control it. Most likely, you will have to do your own air sampling to determine your exposure levels.”
Crystalline silica is a natural part of the earth’s crust and is a basic component of sand and gravel. Silicosis is a disease of the lungs caused by breathing in dust containing crystalline silica particles, according to OSHA.
Significant exposure to crystalline silica can come as the result of sandblasting to remove paint or rust from stone buildings, metal bridges, tanks and other surfaces. However, it can also be created when power tools cut, grind or chip through granite and other materials containing silica, and emit a dust cloud.
Walbridge’s Health, Safety & Environmental team is working closely with specialists from Travelers, the company’s insurance firm, to address the issue. It requires a combination of engineering controls and altering work practices to reduce exposure to below the permissible exposure level (PEL), and, ideally, below the action level. If these controls do not lower exposure enough, then personal protective equipment (PPE) may be needed as well.
Sampling current worksites is the starting point. The Industrial Hygiene Lab at Travelers has equipment available to loan to clients so they can do their own sampling. Travelers can also assist with procedures to follow for consistent monitoring and reporting information to a registered laboratory.
OSHA has established Table 1, which includes 18 “common tasks and equipment” where crystalline silica exposure typically occurs. There is list of engineering and work practice control methods, and PPE required to be worn by people performing those tasks.
How work is done will also change. “Tools may have to have integrated means to collect or suppress the dust,” Lindberg said. “There’s no more ‘dry sweeping’ or using compressed air to sweep up on a job site. You’ll have to use a vacuum system.”
The new standard will also put pressure on improving communication between a general contractor (GC) and subcontractors, Lindberg said. An exposure control plan needs to be developed, he said, so the GC “knows where they’re going to get exposure to silica dust on the site.” And “while the GC may not be creating it, if a subcontractor is creating dust that effects another subcontractor, those employees need to be protected. The controlling contractor bears overall responsibility. Companies are going to have to work together on this to make it effective.”
OSHA established the new standard on March 23, 2016, with enforcement for construction starting on Sept. 23, 2017. Individual states have up to six months after adoption of a new federal OSHA standard to adopt an equivalent or more stringent standard of their own.
“We’re working closely with our mega-business units to make sure we address the new standards and that we’re all on the same page,” said Mike Palazzola, Walbridge Director of Safety. “We have completed numerous Silica Awareness Training Sessions involving our project teams and subcontractors. We want to further educate and provide direction to our subcontractor base affected by the standard. The more we can coach up our subcontractors, the easier the transition to compliance will be.”